Luz natural en el interior de los edificios
Un lucernario, también llamado tragaluz o claraboya, es una ventana que se instala en un techo o parte superior de una pared con el objetivo de proporcionar luz natural a una estancia.
La instalación de un lucernario en un edificio proporciona no sólo una luz de calidad, sino que también, si está bien situado, un importante ahorro energético y de calefacción.
Los materiales más utilizados para la creación de lucernarios, son la fibra de vidrio, el cristal y el PVC, aunque en los últimos años el material más instalado, por sus excelentes propiedades, está siendo el policarbonato. Este material ofrece unas características que lo hacen ideal para este tipo de instalaciones: tiene gran resistencia a los impactos, elevados niveles de transmisión de la luz solar, se comporta bien ante la presencia de fuego, es ligero y muy resistente a condiciones atmosféricas adversas. Otra característica importantísima para su uso en lucernarios es que es capaz de eliminar hasta el 99% de los rayos UV, por lo que tiene un gran poder de protección frente a las radiaciones ultravioletas.
El policarbonato que se instala en las claraboyas se encuentra en formato placa y puede ser de color, absolutamente transparente o translúcido, para producir luz difusa.
Para su instalación, es importante que se tenga en cuenta el aislamiento térmico, ya que de lo contrario, el tragaluz puede convertirse en un punto débil para la climatización de un edificio. En caso de que no se pueda asegurar un alto aislamiento térmico, es recomendable que se cree un puente térmico.
Otro aspecto importante que se tendrá que tener en cuenta va a ser el mantenimiento: va a ser necesario que pueda accederse a su parte superior con el objetivo de realizar tareas de mantenimiento y limpieza. Este hecho garantiza a largo plazo los objetivos para los que se instalan este tipo de estructuras.
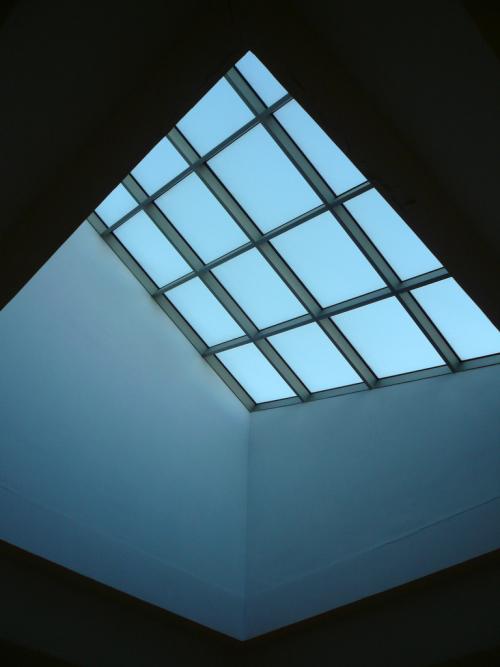
Materiales para la protección pasiva contra incendios
La protección pasiva contra el fuego se sirve de varios materiales que evitanel inicio del fuego, su propagación y se encargan de la protección estructural del edificio, proporcionando garantías de éxito a los equipos de extinción.
Los materiales más habituales para los fines de la protección pasiva son el mortero de perlita y vermiculita, la lana de roca y los paneles de yeso ignífugos especialmente diseñados para tal fin.
El mortero de perlita está compuesto por áridos ligeros de perlita y vermiculita, ligantes hidráulicos, controladores del adormecimiento y material rodante de proyección. La perlita es una roca volcánica vítrea que contiene agua en su molécula. No es tóxica y es incombustible, además de ligera. Lo importante de este material es que incluso a una temperatura de 1.200 ºC sigue manteniendo sus propiedades iniciales. La aplicación del mortero se hace por proyección mediante un sistema de bombeo. Es un sistema muy útil para ingnifugar techos irregulares o con vigas, ya que se adapta absolutamente al relieve que tenga el techo, cubriendo su superfície. Este material permite tiempos de evacuación de entre 120 y 240 minutos, dependiendo del material sobre el que esté proyectado.
La lana de roca es un material que proviene del procesado de una roca basáltica a alta temperatura, a la que se añade durante el proceso una pequeña cantidad de ligante orgánico. El resultado es un material esponjoso de estructura fibrosa, que contiene aire prácticamente inmóvil en su interior. Este material conserva sus propiedades a temperaturas de más de 1000ºC, es termoestable y no produce gases tóxicos
Por último, encontramos tabiquería de yeso. Son paneles a los que se ha añadido al yeso (ya de por sí ignífugo) lana de roca para augmentar su resistencia al fuego. Tienen la ventaja de poderse superponer unos con otros para augmentar su tiempo de resistencia, cosa que los hace muy versátiles.
Estos materiales son sometidos a ensayos muy estrictos en laboratorios acreditados y tienen que cumplir las normativas establecidas por ley. Para su instalación se recomienda, con el fin de garantizar su efectividad, que sean instalados por especialistas.
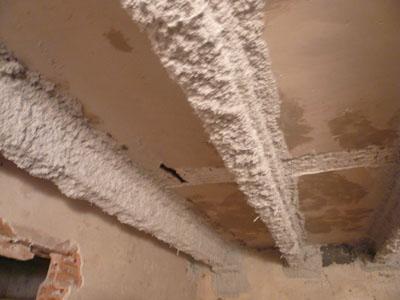
La cubierta: parte esencial del aislamiento de un edificio
Las cubiertas son estructuras de cerramiento exterior superior de los edificios. Su función principal consiste en resguardar el edificio contra los agentes climáticos y aislarlotérmica y acústicamente.
Toda cubierta está formada por una estructura de vigas y pilares (estructura portante) que permite la instalación del resto de materiales que forman la cubierta, distribuyendo las cargas y siendo la base para anclar los materiales de la cimentación y el componente horizontal. Para este componente horizontal se utilizan materiales como el fibrocemento, el panel sandwich o chapas de acero galvanizado y materiales para el aislamiento térmico, que se distribuyen y fijan también a la estructura.
Las cubiertas deben contar con sistemas de recolección de las aguas pluviales para evitar el encharcamiento y deterioro de los materiales que forman la cubierta, evitando las filtraciones al interior del edificio. Para este fin se instalan canalones que distribuyen el agua hasta los bajantes, así como sumideros que comunican con estos bajantes.
Existen diferentes tipos de cubiertas: cubiertas planas, cubiertas inclinadas y cubiertas de doble curvatura o autoportantes.
Las cubiertas planas son cubiertas de eje rectilíneo. Pueden ser transitables, según el tipo de aislamiento que se haya instalado. Este tipo de cubiertas soportan grandes movimientos de dilatación-contracción a causa de las oscilaciones de temperatura a las que están expuestas, por lo que es importante que cuenten con juntas de dilatación para evitar su deterioro.
Las cubiertas inclinadas planas están formadas por una o más pendientes (“aguas”) con unos determinados grados de inclinación. Permiten la evacuación rápida de las aguas pluviales y nieve y su exposición no perpendicular a los rayos del sol hace que permitan el paso de menos calor al interior del edificio.
Por último, las cubiertas autoportantes son las que pueden ser montadas sin una estructura portante. Este tipo de instalaciones se montan sobre un perfil curvado que se apoya sobre las vigas de carga del edificio. Permiten estructuras más longevas y soluciones creativas, por lo que se utilizan bastante en obras públicas.
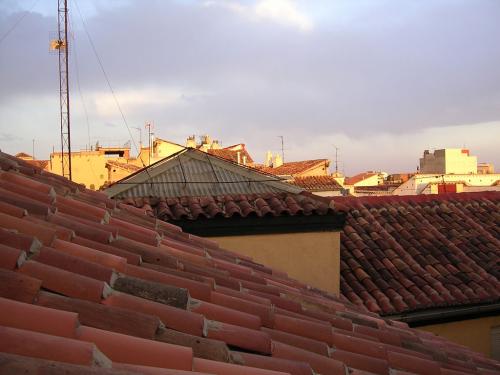
Preparación de una terraza para su impermeabilización
Cuando una terraza es transitable, el uso que se hace de ella, provoca que su deterioro sea mayor y la posibilidad de que aparezcan las humedades mucho mayor que en terrazas o cubiertas no transitables.
Cuando hay que impermeabilizar una terraza lo primero que hay que plantearse es si se va a realizar la operación por encima del solado existente o bien si se va a levantar el solado que que hay. Muchas veces esta elección va a depender del estado del solado y del presupuesto.
En primer lugar va a tenerse que sanear el suelo existente, en el caso que se vaya a conservar. Se trata de eliminar y desinfección normalmente mediante los microorganismos y hongos que van depositándose en el suelo con el tiempo. Normalmente esto se conseguirá mediante una solución de un material especial en agua y la aplicación mediante agua a presión.
A continuación es sumamente importante la reparación y comprobación del estado de las zonas críticas, o zonas que están más expuestas a la degradación y por lo tanto potencialmente zonas por donde se puede filtrar agua. De hecho, son las zonas por donde empiezan a crearse las humedades: juntas con los muros de cerramiento, desagües, fisuras… estas zonas deben ser consolidadas con materiales especiales y restauradas con masillas, en caso necesario.
Una vez realizados estas maniobras es el momento de elegir el sistema de impermeabilizado. Puede utilizarse tela asfáltica, membranas especiales de PVC u otros materiales o pinturas impermeabilizantes.
En todo caso, sea cual sea la forma de impermeabilización, es recomendable que el material utilizado sea altamente resistente a los cambios de temperatura, elástico, resistente a las agresiones medioambientales, impermeable al agua, permeable al vapor, resistente a la alcalinidad del soporte y de fácil mantenimiento. Mediante el uso de cualquier material que reúna estas características se puede asegurar el éxito de la impermeabilización y evitar humedades posteriores.
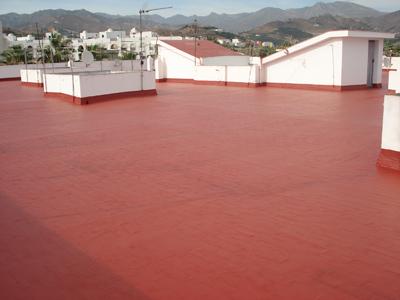
Aislamientos acústicos del tipo "masa-muelle-masa"
Aislar acústicamente no es una tarea fácil. El aislamiento acústico se consigue principalmente gracias a la combinación de materiales de densidad superior a los 300 quilogramos por metro cúbico, que rompan la onda sonora y que la absorban. Un sistema muy utilizado es el llamado masa-muelle-masa: la masa se consigue con un material de alta densidad, seguido de una capa de material elástico que frene la onda (muelle) y finalmente otra capa de material denso (masa). De esta forma se consigue “filtrar” la onda sonora en su sucesivo paso por los diferentes materiales. En algunos casos, para finalizar este proceso es necesario un último material absorbente y que la instalación no tenga contacto directo con la estructura del edificio, para evitar la transmisión de la onda sonora a las vigas. Esto se consigue mediante silentblocks que amortiguan la onda antes de llegar a la estructura.
Los materiales habitualmente más utilizados para una insonorización son las placas de yeso tipo Pladur y la lana de roca, aunque existen también otros materiales especialmente creados para la insonorización.
La lana de roca es un material fabricado a partir de roca volcánica. Tiene propiedades ignífugas y protectoras del calor, y gracias a su estructura multidireccional y elástica frena el movimiento de las partículas de aire y frena la onda sonora. Este material constituye la “masa” de la que se ha hablado anteriormente.
Pero no es únicamente una cuestión de materiales y disposición de éstos: es necesario que las juntas de instalación de estos materiales sean absolutamente estancas: puede imaginarse el sonido como un líquido que puede salir por cualquier apertura que tenga su recipiente, si alguna junta no está bien sellada, el sonido saldrá por esta apertura y la insonorización habrá perdido su utilidad.

Uralita, el fibrocemento de la Barcelona de los 90
“Uralita” es el nombre comercial con que se popularizaron hasta la década de los 90 las placas de fibrocemento. El fibrocemento es un material que se utilizaba en construcción, normalmente para cubiertas y depósitos de agua por las propiedades y disposición de las fibras del amianto que contiene.Así, este material además de ser ignífugo y resistente al ataque químico, ofrecía gran resistencia mecánica a movimientos de compresión y tensión y no era electrotransmisor. El amianto, o asbesto, es el principal causante de afecciones pulmonares, como la asbestosis, y está directamente relacionado con algunos tipos de cáncer.Este material, potencialmente nocivo, es tóxico por inhalación, por lo que, si no se manipulan instalaciones de este material, el riesgo de enfermedad es prácticamente inexistente. De lo contrario, con la rotura o manipulación del fibrocemento, las fibras de amianto se desprenden y se pueden desplazar por el aire, inhalándose peligrosamente.En España, está prohibida la fabricación de productos a partir de este material desde Diciembre de 2001, y desde el 2002, su comercialización. Así mismo, en la rehabilitación de edificios donde existe este material, es obligatorio que los productos de fibrocemento sean retirados por una empresa especialista en la retirada y tratamiento del amianto.La retirada de este material debe efectuarse con medidas de extrema seguridad y es necesario que los residuos sean depositados en vertederos especializados, con el fin de evitar la contaminación ambiental y las consecuencias para la salud de las personas, por lo que es sumamente importante que su manipulación sea efectuada por profesionales especializados y no por particulares.

Uralita, el fibrocemento de la Barcelona de los 90
“Uralita” es el nombre comercial con que se popularizaron hasta la década de los 90 las placas de fibrocemento. El fibrocemento es un material que se utilizaba en construcción, normalmente para cubiertas y depósitos de agua por las propiedades y disposición de las fibras del amianto que contiene.Así, este material además de ser ignífugo y resistente al ataque químico, ofrecía gran resistencia mecánica a movimientos de compresión y tensión y no era electrotransmisor. El amianto, o asbesto, es el principal causante de afecciones pulmonares, como la asbestosis, y está directamente relacionado con algunos tipos de cáncer.Este material, potencialmente nocivo, es tóxico por inhalación, por lo que, si no se manipulan instalaciones de este material, el riesgo de enfermedad es prácticamente inexistente. De lo contrario, con la rotura o manipulación del fibrocemento, las fibras de amianto se desprenden y se pueden desplazar por el aire, inhalándose peligrosamente.En España, está prohibida la fabricación de productos a partir de este material desde Diciembre de 2001, y desde el 2002, su comercialización. Así mismo, en la rehabilitación de edificios donde existe este material, es obligatorio que los productos de fibrocemento sean retirados por una empresa especialista en la retirada y tratamiento del amianto.La retirada de este material debe efectuarse con medidas de extrema seguridad y es necesario que los residuos sean depositados en vertederos especializados, con el fin de evitar la contaminación ambiental y las consecuencias para la salud de las personas, por lo que es sumamente importante que su manipulación sea efectuada por profesionales especializados y no por particulares.
